As reported in a Maritime Reporter and Engineering News February 2022 article, Offshore Wind Development Gains Speed in the United States, the offshore wind (OSW) market is beginning to heat up. The White House policy target of 30 GW of offshore wind power by 2030, increasing the Bureau of Ocean Energy Management’s (BOEM’s) leasing awards, and permitting target approval dates, together with more state energy procurement awards, are creating demand for more port infrastructure, Jones Act compliant vessels, and manufacturing facilities for wind farm components.
Recently a study (Parkison, Sara B. and Willett Kempton, “Marshalling Ports Required to Meet US Offshore Wind Power Policy Targets” Energy Policy, Volume 163, April 2022), concluded that supply (and storage area) of US marshalling port infrastructure for offshore wind projects is insufficient to meet the immediate demand by 2023 and far short of that needed for projected policy targets through 2050.
The challenge ahead for the U.S. market is to develop enough marshalling area for long-term, large-scale, and economically efficient use by the OSW industry. The demand for investing in redeveloping port infrastructure that can enable the logistics of lifting and moving heavy offshore wind power components by specialty vessels is at an all-time high. Federal, state and private funding is becoming available for redeveloping our ports.
GZA has been working on engineering design teams providing geotechnical, marine, and coastal engineering services for port owners, contractors, and OSW developers on several offshore wind ports on the east coast. The geotechnical, marine, and coastal engineering solutions that are available to improve the load capacity of ports and waterfront properties for the OSW industry are discussed.
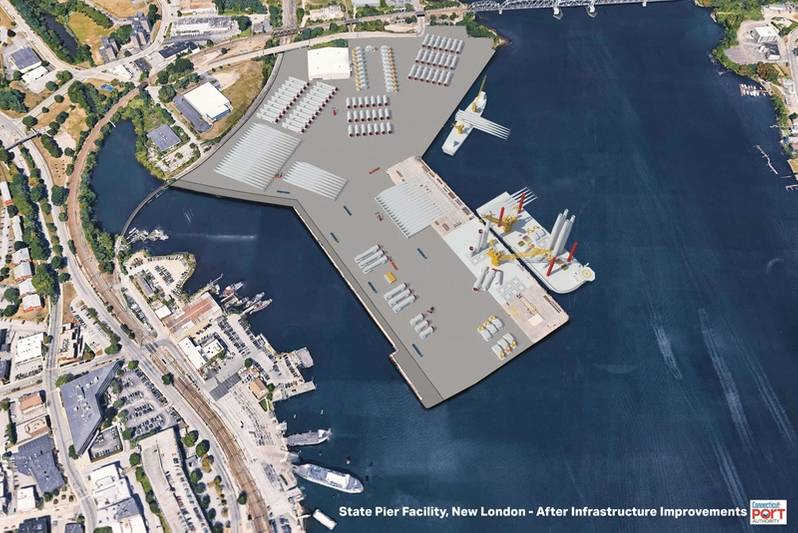
OFFSHORE WIND PORT DEVELOPMENT
Offshore Wind port facilities consist of two areas of concern; a waterfront ship servicing berth with heavy loadout capacity; and an upland area for transport, storage, marshalling, and/or manufacturing of OSW components. The waterfront berth must provide a deep enough dredge elevation to accommodate the transport vessels close to the loadout equipment. Such equipment may include roll on-roll off ramps or high-capacity fixed position or mobile cranes. The transport vessels may also require a prepared bottom or submarine structure to allow spud jacking for hydrodynamic stability. The upland areas must support movement storage, and assembly of the OSW components prior to loadout and transport to the offshore wind farm.
The first OSW terminal in the United States, the New Bedford (Massachusetts) Marine Commerce Terminal, was a completely new, purpose-built facility. It included a cellular bulkhead, a deep dredged berth, a waterside relieving platform for crane support, and an extensive gravel surfaced upland area. More commonly, the future OSW terminals will be rehabilitated under-used or functionally obsolete existing port facilities.
Because of the anticipated high demand and short time frame, numerous existing waterfront facilities are under consideration, in design, or currently under construction (Port of Providence, South Quay-East Providence and Quonset Point, RI, New London and Bridgeport, CT, Salem and Brayton Point, MA, and Paulsboro, NJ). Reuse and repurposing of existing properties can present challenges.
As stated above, the OSW industry has certain requirements that many aging ports currently do not meet. Limited dredge depth, deteriorated bulkheads and quay walls, and limited surface load capacities of pier and wharf structures and adjacent upland areas need to be addressed. Because the large-scale development needs of the OSW industry is for a limited time frame (10 to 20 years) within a particular local, short to medium term fixes may be in order. A new relieving platform may be able to span over an old bulkhead, seawall, or rip-rap slope to reach deeper water. Relatively inexpensive isolated mooring dolphins might accomplish the same goal. An isolated pile supported crane platform may allow loading and off-loading without requiring heavy surface capacity adjacent to existing waterfront structures. Every existing marine facility has a combination of structural, geotechnical, and coastal issues that need to be holistically assessed.
Upland areas also have concerns with storage capacity, topography, elevation, and most importantly subsurface conditions. Limited storage space may be able to be increased by procuring additional adjacent parcels. Adjusting surface elevation and topography is easy to accomplish if the subsurface soil conditions are adequate. Poor subsurface soil conditions can often be improved, at reasonable costs, using standard earthwork or the right ground improvement techniques. Designing for actual component and vehicle ground load pressures rather than unrealistically high “developer requested” uniform ground pressures can result in substantial cost savings to a project.
Every existing port facility has its own set of positive and negative conditions. As the song goes: You got to accentuate the positive, Eliminate the negative, Latch on to the affirmative, and Don’t (ever, ever, ever) mess with Mr. in-between.